Roboterbasiertes Bohren und Nieten
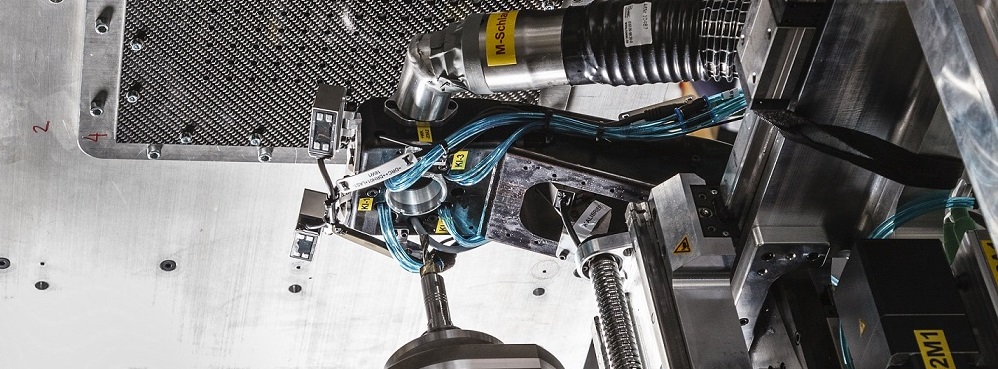
Ziel des Projekts Robotic Drilling and Riveting war es, Technologien zu entwickeln, die ein roboterbasiertes Bohren und Nieten mit hoher Genauigkeit ermöglichen. Insbesondere die Positionierung, wie die Orthogonalität der Bohrlöcher, standen hierbei im Vordergrund. Es wurden Versuche mit verschiedenen Materialien, wie Aluminium, Titan, Kohlefaserverbundkunststoffen und gemischten Stacks dieser Materialien durchgeführt.
Verbesserung und Gewährleistung von Genauigkeitsanforderungen
In der Luft- und Raumfahrt sowie im Automotive Bereich sind Bohren und Nieten nach wie vor zentrale Prozessschritte. Insbesondere im Luft- und Rahmfahrtbereich gelten hohe Qualitätsanforderungen an die Positionierung und Orthogonalität der Bohrlocher. Typische Werte aus dem Luftfahrtbereich sind +/- 0,5 mm Genauigkeit für die Bohrlochposition und 0,5° Genauigkeit für die Orthogonalität.
Im Gegensatz zu Werkzeugmaschinen bietet roboterbasiertes Bohren und Nieten eine höhere Flexiblität und hierdurch auch höhere Geschwindigkeit bei komplexen Bauteilstrukturen. Ziele des Projekts war es, einen End-Effektor für einen Roboter zu konstruieren, der mit entsprechender Sensorik ausgestattet ist, um die hohen Genauigkeitsanforderungen der Luftfahrtbranche zu gewährleisten. Auf die Verwendung externer Messsysteme, wie Lasertracker, wurde hierbei zugunsten einer höheren Flexibilität bewusst verzichtet.
Projektablauf
Für die Umsetzung des Projekts wurde zusammen mit der Firma Lübbering ein End-Effektor mit geeigneter Sensorik konstruiert. Zu der verwendeten Sensorik gehören: Laserdistanzsensoren, pneumatische Abstandssensoren und ein 2D Kameraystem mit Dunkfeld- und koaxialer Beleuchtung. Diese Sensoren wurden einerseits zur Referenzierung am Bauteil und andererseits zur Sicherstellung der Orthogonalität der Bohrlocher eingesetzt. Um die Bohrlochposition im Nachgang an die Referenzierung sicherzustellen, wurden verschiedene Verfahren zur Genauigkeitssteigerung der Absolutgenauigkeit des Roboters eingesetzt.
Die Umsetzung wurde mit einem Testaufbau und verschiedenen Materialien, wie Aluminium, Titan, Kohlefaserverbundkunststoffen und gemischten Stacks dieser Materialien validiert. Die Versuchsreihe hat eine durchschnittliche Positionsabweichung von 0,285 mm und Orthogonalitätsabweichung von 0,27° ergeben.
Projektnutzen
- Höhere Flexibilität im Vergleich zu Werkzeugmaschinen
- Höhere Geschwindigkeit im Vergleich zur manuellen Fertigung bei schwierigen Zugänglichkeiten
- Verbesserte Genauigkeit der roboterbasierten Fertigung
- Unabhängigkeit von externen Messsystemen, wie Lasertrackern
Beteiligte Industriepartner
- Broetje-Automation Assembly & Turnkey Systems GmbH
- Johannes Lübbering GmbH